Schlauchreifen: Unterschied zwischen den Versionen
>Jeeves KKeine Bearbeitungszusammenfassung |
>Jeeves KKeine Bearbeitungszusammenfassung |
||
(2 dazwischenliegende Versionen von einem anderen Benutzer werden nicht angezeigt) | |||
Zeile 11: | Zeile 11: | ||
* [[Pneumant]] (ab 1977) | * [[Pneumant]] (ab 1977) | ||
Von 1972 bis 1976 | Von 1972 bis 1976 wurden Schlauchreifen sowohl mit [[Kowalit]] (Prägung) und auch [[Pneumant]] (Stempel) gekennzeichnet, da die Marke [[Kowalit]] einen guten Ruf genoss. Als Verbindung findet sich der Slogan ''"KOWALIT - der Schlauchreifen von PNEUMANT"''.<br> | ||
Der international gute Ruf der [[Kowalit]]-Schlauchreifen geht vor allem auf die Erfolge der DDR-Mannschaften bei den großen Radrennen der 1950er Jahre zurück, da diese auf serienmäßigen Reifen errungen wurden. Deshalb und vermutlich auch wegen des guten Preis-Leistungs-Verhältnisses wurden die Reifen in großer Zahl weltweit exportiert. | Der international gute Ruf der [[Kowalit]]-Schlauchreifen geht vor allem auf die Erfolge der DDR-Mannschaften bei den großen Radrennen der 1950er Jahre zurück, da diese auf serienmäßigen Reifen errungen wurden. Deshalb und vermutlich auch wegen des guten Preis-Leistungs-Verhältnisses wurden die Reifen in großer Zahl weltweit exportiert. | ||
Zeile 201: | Zeile 201: | ||
*''Vulkanisieren.'' | *''Vulkanisieren.'' | ||
''Parallel dazu läuft die | ''Parallel dazu läuft die Luftschlauchfertigung. Die Endstufen sind dann das Einnähen des Luftschlauches und das Auflegen des Nahtschutzbandes.''<br> | ||
''Der Spulprozess gewährleistet den Kowalit-Schlauchreifen eine absolut gleichmäßige Fadenlänge in der Reifenkarkasse und vermeidet Unterschiede in der Fadendichte. Auch wird die Wellenbildung im Kordfadenverlauf unterbunden. In solcher Baumwollkordverband erlaubt eine Belastbarkeit in der Karkasse bis zu 30 at Innendruck bei einem Reifendruck von 4 bis 6 at im Einsatz.''<br> | ''Der Spulprozess gewährleistet den Kowalit-Schlauchreifen eine absolut gleichmäßige Fadenlänge in der Reifenkarkasse und vermeidet Unterschiede in der Fadendichte. Auch wird die Wellenbildung im Kordfadenverlauf unterbunden. In solcher Baumwollkordverband erlaubt eine Belastbarkeit in der Karkasse bis zu 30 at Innendruck bei einem Reifendruck von 4 bis 6 at im Einsatz.''<br> | ||
''Der nächste Arbeitsvorgang ist das Duplieren. Nach dem Gummieren der Kordhülle mit Naturkautschuklösung wird der Kord so vom Spuldorn geschnitten, daß die Fäden zur späteren Reifenlaufrichtung in einem Winkel von 45 Grad liegen. Durch Falten des Kordstreifens in der Längsrichtung entsteht ein Kordverband, in dem beide Lagen im Winkel von 90 Grad zueinander und im Winkel von 45 Grad zur Laufrichtung liegen. Diese Anordnung sichert maximale Festigkeit bei großer Elastizität und Seitenstabilität.''<br> | ''Der nächste Arbeitsvorgang ist das Duplieren. Nach dem Gummieren der Kordhülle mit Naturkautschuklösung wird der Kord so vom Spuldorn geschnitten, daß die Fäden zur späteren Reifenlaufrichtung in einem Winkel von 45 Grad liegen. Durch Falten des Kordstreifens in der Längsrichtung entsteht ein Kordverband, in dem beide Lagen im Winkel von 90 Grad zueinander und im Winkel von 45 Grad zur Laufrichtung liegen. Diese Anordnung sichert maximale Festigkeit bei großer Elastizität und Seitenstabilität.''<br> | ||
Zeile 216: | Zeile 216: | ||
==Montage== | ==Montage== | ||
Im Vergleich zu den Drahtreifen ist die Montage von Schlauchreifen | Im Vergleich zu den Drahtreifen ist die Montage von Schlauchreifen aufwendig. Zunächst werden spezielle [[Felgen]] benötigt, die dem Reifen eine durchgehende Auflagefläche - das sogenannte Felgenbett - bieten. Dieses Felgenbett ist zudem konkav gekrümmt und auf den Außenradius des röhrenförmigen Schlauchreifens abgestimmt. Zwar hält sich der straff aufgepumpte Schlauchreifen bereits aufgrund seiner Form in der Felge, doch können die seitlich wirkenden Kräfte bei einer Kurvenfahrt dazu führen, dass er von der Felge "rollt". Um das zu verhindern, muss der Schlauchreifen mit der Felge verklebt werden.<br> | ||
Dazu finden zwei verschiedene Klebemittelarten ihre Anwendung: | Dazu finden zwei verschiedene Klebemittelarten ihre Anwendung: | ||
Aktuelle Version vom 13. November 2018, 20:28 Uhr
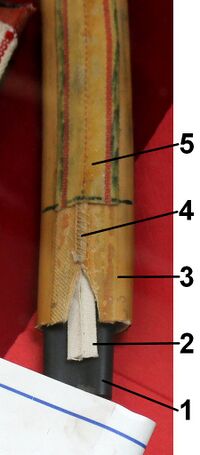
Grundsätzliches
Schlauchreifen stellen eine besondere Variante von Fahrradreifen dar. Sie bestehen wie die üblichen Drahtreifen aus einem Mantel bzw. Decke und einem Schlauch, aber die beiden Teile werden hier nicht erst durch die Montage auf einer Felge zu einer funktionstüchtigen Einheit. Stattdessen umschließt die Decke den ganzen Umfang des Schlauchs und ist auf der Innenseite zusammengenäht. Diese Bauart ermöglicht hohe Reifendrücke und damit sehr gute Leichtlaufeigenschaften in Verbindung mit einem geringen Gewicht.
Verwendung finden Schlauchreifen bei Straßen- und Bahnrennrädern sowie bei Saalsporträdern.
Hersteller
Die Schlauchreifen für die DDR-Fahrradindustrie wurden beinahe ausnahmslos in Waltershausen mit einem hohen Maß an Handarbeit produziert, wurden aber, u.a. wegen der Umbenennung des entsprechenden Werkes, unter verschiedenen Markennamen angeboten:
Von 1972 bis 1976 wurden Schlauchreifen sowohl mit Kowalit (Prägung) und auch Pneumant (Stempel) gekennzeichnet, da die Marke Kowalit einen guten Ruf genoss. Als Verbindung findet sich der Slogan "KOWALIT - der Schlauchreifen von PNEUMANT".
Der international gute Ruf der Kowalit-Schlauchreifen geht vor allem auf die Erfolge der DDR-Mannschaften bei den großen Radrennen der 1950er Jahre zurück, da diese auf serienmäßigen Reifen errungen wurden. Deshalb und vermutlich auch wegen des guten Preis-Leistungs-Verhältnisses wurden die Reifen in großer Zahl weltweit exportiert.
Für das Jahr 1948 ist die Produktion von Schlauchreifen auch für die private Firma Werner Horn aus Halle (Saale) belegt.
Profile und Größen
Passend zu den verschiedenen Disziplinen des Radsports gab es auch Reifen in den verschiedensten Ausführungen und Dimensionen. Kataloge verschiedener Jahre nennen zudem unterschiedliche Gewichte derselben Typen.
Typ | Größe | Profil | Beschreibung | Gewicht | Produziert von... bis... |
---|---|---|---|---|---|
27" × 1" | Längsrillenprofil | Besonders leichter, schmaler Reifen für Kriteriums-/Rundkursrennen |
ca. 260 bis 280 g (1959, 1961) 240 g (1968) |
Ab spätestens 1959, nicht vor 1956 | |
27" × 1" | Längsrillenprofil | Besonders leichter, schmaler Reifen für Kriteriums-/Rundkursrennen | 220 g (1980) | Ab spätestens 1980 | |
27" × 1" | Längsrillenprofil | Besonders leichter, schmaler Reifen mit Karkasse aus Naturseide für Kriteriums-/Rundkursrennen |
220 g (1980) | Ab spätestens 1980 | |
27" × 1 1/16" | Längsrillenprofil | Universalschlauchreifen für Trainingsfahrten, Jugend- und Tourensport | 400 g (1980) | Ab spätestens 1980 | |
27" × 1 1/8" | Längsrillenprofil oder Fischgrätprofil | Üblicher Reifen für Straßenrennen | ca. 340 gr (1959, 1961) 275 g (1968, 1980) |
Ab spätestens 1956, bis mindestens 1980 | |
27" × 1 1/16" | Längsrillenprofil oder Fischgrätprofil | Üblicher Reifen für Straßenrennen | 295 g (1968) | Ab spätestens 1968, nicht vor 1961 | |
27" × 1 1/4" | Längsrillenprofil | Robuster Reifen für Trainingsfahrten | ca. 400g (1959, 1961) | Ab Ende 1955, bis längstens 1968 | |
27" × 1 1/8" | Fischgrätprofil | Robuster Reifen für Trainingsfahrten | ca. 400g (1959) 330 g (1968) |
Ab spätestens 1959, bis mind. 1968 | |
27" × 1 1/8" | Rautenmuster ("diamonds") | Allround-Querfeldein-Reifen | 370 g (1980) | Ab spätestens 1980 | |
27" × 1 1/8" | Rautenmuster ("diamonds"), zwei verschiedene Stollenprofile | Mit Rautenmuster als Querfeldein-Reifen für Vorderrad, mit Stollenprofilen als Allround-Querfeldein-Reifen | ca. 350 bis 380 g (1959) 350 g (1961) 400 g (1968) |
Ab spätestens 1959, bis längstens 1980 | |
27" × 1 1/8" | Schaufelförmigen Elemente für wenig Schlupf auf weichem Untergrund | Querfeldein-Reifen für Hinterrad | ca. 350 bis 380 g (1959, 1961) | Ab spätestens 1959, bis längstens 1980 | |
27" × 1" | Ohne Profil ("slicks"), um 1980 auch mit feinem Waffelprofil | Bahnradreifen für Holzrennbahnen | ca. 190 bis 220 g (1959, 1961) 180 g (1968) 220 g (1980) |
Ab spätestens 1959, bis mindestens 1980 | |
27" × 1" | Feines Waffelprofil | Bahnradreifen mit Karkasse aus Naturseide für Holzrennbahnen | 200 g (1980) | Ab spätestens 1980 | |
27" × 1" | Ohne Profil ("slicks") | Ultraleichte Bahnradreifen | 150 g (1968) | Ab spätestens 1968, bis längstens 1980 | |
27" × 1" | Vrmtl. ohne Profil ("slicks") | Bahnradreifen für Zementrennbahnen | ?? | Ab spätestens 1956, bis längstens 1959 | |
27" × 1" | Ohne Profil ("slicks") | Bahnradreifen für Zementrennbahnen | ca. 250 bis 270 g (1959, 1961) 200 g (1968) 220 g (1980) |
Ab spätestens 1959, bis mindestens 1980 | |
27" × 1" | Ohne Profil ("slicks") | Bahnradreifen mit Karkasse aus Naturseide für Zementrennbahnen | 200 g (1980) | Ab spätestens 1980 | |
27" × 1 1/16" | Querriffelung, im Zenit durch dünne Längsrillen unterbrochen | Für Tandem- und Bahnwettbewerbe und Zeitfahren | 240 g (1980) | Ab spätestens 1980 | |
27" × 1" | Längs- und Fischrätprofil | Tourenreifen für die Radsportjugend | 350 g (1968) | Ab spätestens 1968, bis längstens 1980 | |
26" × 1" | Feines Waffelprofil | Für Saalmaschinen (Radball- und Reigenräder) | 470 g (1980) | Ab spätestens 1980 | |
26" × 1 1/4" | Feines Waffelprofil | Für Saalmaschinen (Radball- und Reigenräder) | ca. 450 g (1959, 1961) 440 g (1968) 400 g (1980) |
Ab spätestens 1959, bis mindestens 1980 | |
26" × 1 1/2" | Feines Waffelprofil | Für Saalmaschinen (Radball- und Reigenräder) | ca. 600 g (1959, 1961) 530 g (1968) |
Ab spätestens 1956, bis längstens 1980 |
Herstellung
Ein Prospekt des VEB Gummikombinat Thüringen von 1968 gibt Auskunft über Material und Herstellungsprozesse von KOWALIT-Schlauchreifen:
"Meister im Mixen von Rezepturen sind die Fachleute an den Mischanlagen des Gummikombinats Thüringen, denn erst die richtige Mischung von Naturkautschuk mit den verschiedenen Weichmacher- und Vulkanisationsmitteln erbringt den Gummi, der mit seinen guten Eigenschaften zur Herstellung von Schlauchreifen geeignet ist. Zu diesen guten Eigenschaften zählen Abriebfestigkeit, Elastizität sowie Hitze-, Kälte- Öl- und Säurebeständigkeit. Da aber das Bessere der Feind des Guten ist, gibt es bei Kowalit in der Reifenentwicklung keinen Stillstand, ständig werden die Mischungen überprüft und neue Rezepturen erprobt. Für die Flankenstreifen und Protektoren der Kowalit-Schlauchreifen kommen nur reine Naturkautschuk-Mischungen bester Qualität zur Verwendung. Ebenso sind alle Luftschläuche (mit Ausnahme der Hallensportreifen und des Tourenreifen) Latexartikel aus hundertprozentigem Naturkautschuk. Auch bei der Karkassenherstellung gelangen nur hochwertige Rohstoffe zur Verarbeitung. Die Reifenkarkassen bestehen deshalb aus langstapliger ägyptischer Baumwolle oder feinster Naturseide. Alle Materialien unterliegen bereits vor der Verarbeitung einer besonders scharfen Kontrolle.
Adäquat der Qualität der Rohstoffe ist die moderne Verarbeitungstechnologie bei Kowalit. Hier vereinigen sich traditionelle Handarbeit und neuzeitliche Regelungstechnik zu einer harmonischen Einheit. Die Fertigung der Kowalit-Schlauchreifen vollzieht sich in den Hauptstufen
- Spulen,
- Dublieren,
- Beschneiden,
- Buggen,
- Vulkanisieren.
Parallel dazu läuft die Luftschlauchfertigung. Die Endstufen sind dann das Einnähen des Luftschlauches und das Auflegen des Nahtschutzbandes.
Der Spulprozess gewährleistet den Kowalit-Schlauchreifen eine absolut gleichmäßige Fadenlänge in der Reifenkarkasse und vermeidet Unterschiede in der Fadendichte. Auch wird die Wellenbildung im Kordfadenverlauf unterbunden. In solcher Baumwollkordverband erlaubt eine Belastbarkeit in der Karkasse bis zu 30 at Innendruck bei einem Reifendruck von 4 bis 6 at im Einsatz.
Der nächste Arbeitsvorgang ist das Duplieren. Nach dem Gummieren der Kordhülle mit Naturkautschuklösung wird der Kord so vom Spuldorn geschnitten, daß die Fäden zur späteren Reifenlaufrichtung in einem Winkel von 45 Grad liegen. Durch Falten des Kordstreifens in der Längsrichtung entsteht ein Kordverband, in dem beide Lagen im Winkel von 90 Grad zueinander und im Winkel von 45 Grad zur Laufrichtung liegen. Diese Anordnung sichert maximale Festigkeit bei großer Elastizität und Seitenstabilität.
Es folgt das Beschneiden und Buggen. Das genaue Zuschneiden des Rohlings und das Umlegen der Hüllenränder geschieht maschinell und auf beiden Seiten gleichzeitig. Daraus resultiert eine konstante Breite der Karkasse, die für die Rundlaufeigenschaften von großer Bedeutung ist. Das Umbuggen verhindert das Herausreißen der Nähfäden beim späteren Nähprozeß.
Die Vulkanisation der meist dreiteiligen Protektoren mit ihren Textilverstärkungen, Flankenstreifen und Laufflächen in programmgesteuerten Bag-o-matic-Einzelheizern garantiert eine genaue Einhaltung der Vulkanisationsbedingungen (Temperatur, Druck, Zeit) und eine gleichmäßige Beanspruchung der Reifenhülle.
Nach der Fertigung der einteiligen Luftschläuche aus Naturkautschuklatex mit eingeschraubten vernickelten Messingventilen erfolgt das Einnähen der Luftschläuche in die Reifenhüllen. Eine Besonderheit bei der Produktion von Kowalit-Schlauchreifen ist das Einnähen des Nahtschutzbandes in die Naht bei Verwendung einer zweifädigen Überwendlich-Naht. Damit wird jedes Verzugsmoment auf den Reifen vermieden. Diese Fertigungsmethode trägt zur Erhöhung der Rundlaufeigenschaften bei. Das Auflegen des durch seine Körperwebart dehnbaren Nahtschutzbandes erfolgt mittels hochgezüchteter Klebelösungen von Hand. [...]"
Montage
Im Vergleich zu den Drahtreifen ist die Montage von Schlauchreifen aufwendig. Zunächst werden spezielle Felgen benötigt, die dem Reifen eine durchgehende Auflagefläche - das sogenannte Felgenbett - bieten. Dieses Felgenbett ist zudem konkav gekrümmt und auf den Außenradius des röhrenförmigen Schlauchreifens abgestimmt. Zwar hält sich der straff aufgepumpte Schlauchreifen bereits aufgrund seiner Form in der Felge, doch können die seitlich wirkenden Kräfte bei einer Kurvenfahrt dazu führen, dass er von der Felge "rollt". Um das zu verhindern, muss der Schlauchreifen mit der Felge verklebt werden.
Dazu finden zwei verschiedene Klebemittelarten ihre Anwendung:
Die ältere ist das Verkleben mit einem speziellen Kleber, dem sogenannten Schlauchreifenkitt. Dieser wird mit einem Pinsel auf das Felgenbett und das Nahtschutzband des Reifens gestrichen und anschließend wird der Reifen auf die Felge aufgezogen.
Vorteilhaft bei dieser Methode ist, dass der Kleber nicht sofort anzieht und sich der Reifen gut ausrichten und auf der Felge zentrieren lässt. Nachteilig ist, dass diese Variante ein hohes Maß an Geschick erfordert, um den später straff sitzenden Schlauchreifen in des Felgenbett zu ziehen, ohne den Kleber auf den Flanken des Reifens oder den Bremsflächen der Felgen zu verteilen.
Dieser Aufwand entfällt bei der zweiten Methode, bei der statt des flüssigen Klebers ein doppelseitig klebendes Band zum Einsatz kommt, das zunächst ausgehend vom Ventilloch in das Felgenbett geklebt wird. Anschließend werden die ersten Zentimeter des Schutzstreifens abgezogen und nach außen geklappt. Danach wird der Schlauchreifen aufgezogen, locker aufgepumpt und ausgerichtet. Der Schutzstreifen wird dann seitlich zwischen Reifen und Felge herausgezogen.
Nachträgliche Korrekturen sind dabei aber nur noch schwer möglich. Hinzukommt ein negativer Effekt, der sich auf eine Eigenart der DDR-Schlauchreifenfelgen zurückführen lässt. Da das Klebeband die im Felgenbett liegenden Speichennippelköpfe nur überspannt, anstatt die durch sie entstehenden Niveauunterschiede auszugleichen, liegen so verklebte Schlauchreifen häufig unsauber auf der Felge oder lösen sich im Bereich der Nippel sogar von dieser ab. Vermeiden lässt sich das, indem das Klebeband vor und nach jedem Nippelkopf sorgfältig auf das Felgenbett geklebt wird.
Bernol-Schlauchreifenkitt
(1950er Jahre; noch immer flüssig).
Reparatur
Die Reparatur von Schlauchreifen war und ist vergleichsweise aufwendig. In der zeitgenössischen Literatur gab es daher Hinweise zur fachgerechten Reparatur für den Laien. Daneben boten mehrere Firmen professionelle Reparaturen an und warben dafür ausgiebig in Radsportzeitschriften.